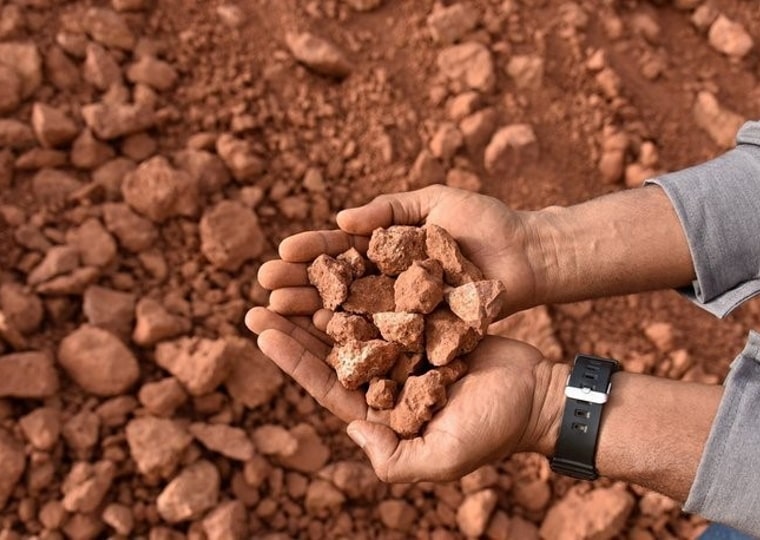
Aluminum is used in the production of millions of different products in many branches of industry and has a very important place in the world economy. It is indispensable in the automotive, aerospace and defense industries that require lightness and high strength properties. It also finds wide use in the construction and furniture industry where aesthetics is at the forefront.
GENERAL FEATURES
- Aluminum, which is found in nature as bauxite ore, is one of the most abundant elements in the world.
- It is obtained by decomposition by electrolysis method.
- Pure aluminum is a soft metal, but its alloys are about 15 times stronger than its pure form.
- Its weight is about one-third that of steel or copper.
- It can be easily forged, machined and shaped.
- It has very high corrosion resistance.
- It is non-toxic and non-magnetic.
- Aluminum is an environmentally friendly metal and can be recycled endlessly.
- The energy used for recycling is approximately 5% of the energy used for its initial recovery.
Ability to Recycle
Aluminum is forever durable and one of nature's best friends. Therefore, it is your best friend.
Formability
Aluminum, with its superior malleability, allows you to shape it into almost any product you can imagine.
Weight
With about 1/3 the density of steel (2,700 kg/m³), aluminum is a super light material. For this reason, it continues to replace different materials in all sectors.
Resistance
Aluminum alloys have tensile strengths between 70 and 700 MPa. Unlike the high-temperature machining of steel, aluminum's strength increases at low temperatures. This makes aluminum the natural choice in many places.
Processing
The versatility of working with aluminum is incredible. Features such as grinding, drilling, cutting and bending are among the most common methods of forming aluminum. In addition, the energy input during machining is also low, and in other words, it is more environmentally friendly.
Aluminum is Strong
Aluminum is extremely light due to its low density. But extrusions can be made strong and durable. This is all about technical knowledge and processing.
Corrosion Resistance
Aluminum reacts with oxygen in the air to form an extremely thin oxide layer. Although this layer is only a few hundred microns thick, it is dense and provides excellent corrosion protection. This layer can repair itself when damaged.
History
Although it is known that Friedrich Wöhler was the first person to decompose aluminum by mixing anhydrous aluminum chloride with potassium in 1827, it was produced in an impure form by Hans Christian Øersted, a Danish physicist and chemist, about two years ago. Therefore, in the chemistry literature, Øersted's name is mentioned as the person who discovered aluminum. French Henri Saint-Claire Deville developed Wöhler's method in 1846 by using sodium instead of the more expensive potassium.
In 1886, the American Charles Martin Hall applied for a patent on the production of aluminum by an electrolytic process. In the same year, completely unaware of Hall's invention, the French Paul Héroult developed the same technique in Europe. For this reason, the Hall-Heroult process, named after two scientists, is the basic method used all over the world in the extraction of aluminum from its ore today.
Basic Features
Atomic Number: | 13 |
Element Series: | Metals |
Group, Period, Block: | 13, 3, p |
Atomic Weight: | 26,9815386(8) g/mol |
Electron Arrangement: | Ne 3s2 3p1 |
Electrons Per Energy Level: | 2, 8, 3 |
Physical Features
State of Matter: | Thick |
Intensity: | 2,70 g/cm³ |
Density in Liquid: | 2,375 g/cm³ |
Melting Point: | 933,47 °K (660,32 °C) |
Boiling Point: | 2792 °K (2519 °C) |
Melting Heat: | 10,71 kJ/mol |
Evaporation Heat: | 294,0 kJ/mol |
Heat Capacity: | 24,2 J/(mol•K) |
Atomic Features
Crystal Structure: | Surface centered cubic |
Oxidation Levels: | (3+) (amphoter oxide) |
Electronegativity: | 1,61 Pauling scale |
Ionization Energy: | 577,5 kJ/mol |
Atomic Radius: | 143 pm |
Atomic Radius (hes.): | 118 pm |
Covalent Radius: | 118 pm |
Other Features
Electrical Resistance: | 26,50 nΩ•m (at 20°C) |
Thermal Conductivity: | 237 W/(m•K) |
Thermal Expansion: | 23,1 µm/(m•K) (at 25°C) |
Sound Speed: | 5000 m/s (at 20°C) |
Mohs Hardness: | 2,75 |
Vickers Hardness: | 167 MPa |
Brinell Hardness: | 245 MPa |
Alloys
The mechanical, physical and chemical properties of aluminum alloys vary depending on the alloying elements and microstructure. The most important alloying elements added to aluminum are copper, manganese, silicon, magnesium and zinc.
Aluminum alloys are divided into two groups as forging and casting alloys. Wrought alloys have good plastic deformation ability and can be easily shaped. Most of the aluminum forging and casting alloys can be heat treated.
According to the American aluminum association, aluminum wrought alloys are classified by four letters.
This classification is as follows:
1xxx Series
It has 99% and higher aluminum content. Corrosion resistance, electrical and thermal conductivity are excellent. Its mechanical properties are low. Small increases in strength can be achieved with strain hardening. It is mainly used in the electrical and chemical industries. Welding is possible.
Alloys: 1050, 1060, 1100, 1145, 1200, 1230, 1350 etc.
2xxx Series
The main alloying element is copper. Contains up to 6.3% copper. Other alloying elements, especially magnesium, can also be found. It shows precipitation hardening. They do not have as good corrosion resistance as other aluminum alloys. Weldability is poor to moderate depending on the alloy. The good thing about these series is that they show good resistance at temperatures up to 150°C (300°F). It is widely used in the manufacture of products such as aircraft body and mechanical elements, vehicle body panels, where high strength is required. The 2024 aluminum series is the most common type of aluminum and is effectively used in aircraft design.
Alloys: 2011, 2014, 2017, 2018, 2124, 2219, 2319, 2010, 2030, 2060, 2240, 2420 etc.
3xxx Series
The main alloying element is manganese. It has very good corrosion resistance with excellent deformation and weldability. It is generally not heat treatable, but about 20% of the series contains stronger aluminum alloys than the 1xxx series. It has a typical yield strength of up to 250 MPa. It is used in the manufacture of beverage cans, chemical containers, industrial roofing, curved pipes.
Alloys: 3003, 3004, 3105, 3830, 3850, 3900 etc.
4xxx Series
The main alloying element is silicon (Generally, the Si ratio is up to 12%). If it contains Cu, precipitation can be hardened. They are alloys with low coefficient of thermal expansion, high wear resistance and corrosion resistance. Because these aluminum alloys contain significant amounts of charcoal gray silicon, they are demanded in architectural applications and used in anode oxide coating. They are used in the manufacture of high temperature resistant parts such as pistons, in welded structures, in the manufacture of plates, and also as welding wire and brazing alloy.
Alloys: 4032, 4043, 4145, 4643 etc.
5xxx Series
The main alloying element is magnesium. As the magnesium ratio increases, the hardness and strength increase, but the mosquito net decreases. Addition of up to 5.1% Mg in solution increases the rate of strain hardening. Can be cold hardened for yield strength up to 260 MPa. It has excellent weldability and medium strength. It has high corrosion resistance against sea water and chemicals. It has many uses, especially in the ship industry.
Alloys: 5005, 5049,5052, 5083, 5754 etc.
6xxx Series
The main alloying elements are magnesium and silicon. The combination of Mg and Si allows Mg2Si precipitation hardening. Although not as durable as the 2xxx and 7xxx alloys, the 6xxx series alloys have moderate strength with good formability, weldability, machinability and relatively good corrosion resistance. It is available as sheet, plate, extrusion product. It also has applications such as the 5000 series.
Alloys: 6013, 6052 and 6061 etc.
7xxx Series
Zinc is the main alloying element (contains between 1% and 8% Zn) and is generally used with Mg, Cu and low amounts of Mn and Cr to increase its strength. They are heat treatable and show high strength. 7XXX series is the one with the highest strength of aluminum alloys. It is used where stress corrosion or foiling is a problem. It is often used on airplanes. Copper alloys can be precipitation hardened. There is a range of weldability from bad to very good, depending on the alloy and method.
Alloys: 7075, 7050, 7049, 7100, 7110 etc.
8xxx Series
The main alloying element is lithium, and tin can also be added. Iron and nickel increase strength without any significant loss of electrical conductivity and are used in well-conducting alloys such as 8017. This material, which has been used especially in aircraft and aerospace structures, has good fatigue resistance and good toughness properties. However, production costs are high compared to other Al alloys. It is used in aviation applications.
Alloys: 8006, 8111, 8079, 8500, 8510, 8520 etc.